Proven Tips for Reducing CNC Machining Costs
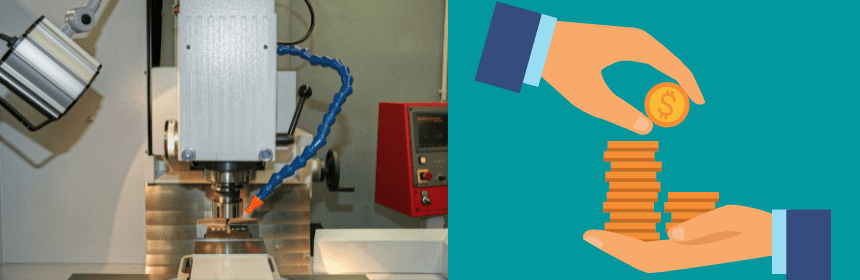
Computer numerical control or CNC machining is the most popular and widely utilized machining technology today. CNC machined parts and components of various types and sizes are preferred across industries to meet their product requirements in terms of speed, accuracy, volume, and precision. Although known for repeatability with consistency and efficiency, CNC machines require a significant investment. Despite this fact, several manufacturers hugely rely on CNC machined parts for efficient and accurate final products. Yet this can’t be overlooked that OEMs look for effective pricing strategies to increase net profit margin while offering products at the most competitive rates to their customers. This is why CNC machining services providers have proven cost-cutting strategies. If you are a manufacturer who is enthusiastically looking for cost-cutting tactics for CNC machining, read this post. These strategies help the manufacturer cut CNC machining costs without compromising on the quality of the product. Stay tuned.
Tactics for Cutting CNC Machining Costs
Optimal utilization of available resources, minimal or zero wastage, and reduced power consumption are three important aspects to make superior quality products by also saving money. Here is the list of important pointers that will help you save on CNC machining costs. Let’s have a look at them.
- One of the efficient and long-term cost-saving strategies is to invest in the appropriate state-of-the-art equipment. While this may seem like an investment, it becomes cost-effective in the long run as advanced equipment consume less power, offer precision and the required flexibility. Also, parts can be machined with tight tolerances if required. CNC machining is a subtractive technique, and hence it ultimately reduces the wastage of material. Less wastage is money saved. Also, only the required amount of material is used for machining, and this mitigates the cost. Technological advancement has increased speed and volume capacities which saves on time. The power consumption costs drop with less machine-running time. All of this leads to reduced time to market of products which adds to the profit.
- Design for manufacturing (DFM) plays a key role in saving CNC machining costs. How? Product designing is an important step in the manufacturing process. The product is designed based on specific requirements, which must be satisfied in the final run. DFM facilitates the most complex designs using compatible and sustainable materials and resources. DFM sets achievable tolerances, avoids curves and cuts, and uses standard drill sizes.
- Next, material bulk purchasing can significantly affect the overall CNC machining costs. If the material is purchased in bulk, then there are high chances of cost reduction. If not, then OEMs need to pay per piece cost. Here, the bill of materials (BOM) needs to be accurate. Also, a robust vendor network helps the service provider procure parts quickly and at the best prices.
- Like bulk material purchasing, high volume production is an effective way of cutting CNC machining costs. Bulk manufacturing is a continuous process, thus, there is no halt time. Switching from one product to another can be done easily, saving machining as well as operational time. However, this depends much on the client requirement in terms of volume. On the other hand, while prototyping requires significant resources to produce just a single part, once finalized, it may save costs during bulk production, in terms of appropriate resource utilization and reduced wastage.
- Reduction in machining operational time also contributes to cost-cutting of CNC machining. It is possible to reduce CNC machining time by adopting seamless machining techniques. In the case of the CNC machining process, the operator needs to set the raw material in the chucks, and it should come out as the final product. However, this is not the case with complex machining parts. This is where part manufacturing makes a significant difference. This can be only possible using tool switching techniques with pre-set program. This, in turn, reduces halt time, machining time as well as power, and overall costs.
The aforementioned are a few proven cost-saving tips for CNC machining. These tips may not only be helpful for OEMs but clients too. If you have a manufacturing unit and looking for high-quality and performance-driven CNC machining services, it is always better to work with experienced players. Brogan & Patrick has vast years of experience in CNC machining and fabrication. With skilled and experienced teams at the helm, the company specializes in offering CNC machining services across industries including medical, aerospace, and military in the USA.
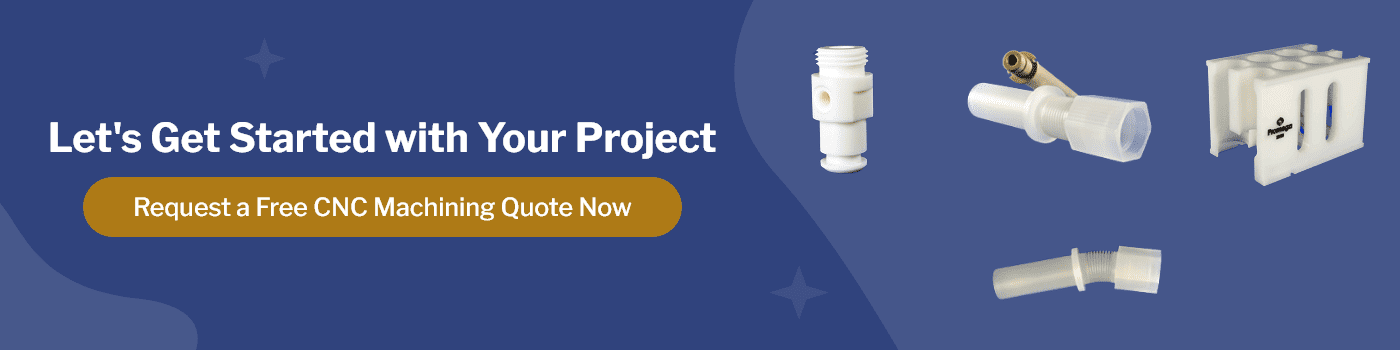