CNC Machining Tolerances: Introduction and Types Explained
CNC machining is the most popular and widely used machining method across industries for creating components and parts using a variety of fabrication techniques. With the advent of technology, these machines have evolved effectively in terms of automated processes, precision, achieving tight tolerances, and much more. When it comes to machining tolerances, most industrial applications has a certain tolerance or acceptance range for the parts or components, in terms of length, dimensions, size, bend radius, and much more. There are some applications wherein this range is rigid, and this means almost no changes in these parameters are acceptable. This is where CNC machining of parts can make a significant difference. Regardless of the demand for precision, CNC machining may create a slight variation in measurements. These variations may occur due to several reasons, such as material or processes used and much more. Therefore, a tolerance level of ± – 0.001 is acceptable in many complex applications. This tolerance limit is usually decided by discussing with the client and accordingly the materials and machining processes are decided. Are you interested to know more about CNC machining tolerances? If yes, then this post discusses the same. So, stay tuned.
CNC Machining Tolerances Types Discussed
Here is the list of some common types of CNC machining tolerance.
- Limit Tolerances: As the name implies, this tolerance type is described as two-dimensional values. One is the lower limit which specifies the minimum acceptable dimension, while another is the upper limit which specifies the maximum acceptable dimension. Any value between these two points is a limit tolerance. For instance, 0.56 – 0.76 mm is an example of a limit tolerance, with 0.56 mm as the upper limit and 0.76 as the lower limit.
- Unilateral Tolerances: In this type of CNC tolerance, only one direction of deviation is permitted, which may be positive or negative based on the specified value. So, if the length of a part is smaller than the specified value, it is followed through in all the parts. Here the value cannot be higher than the specified value in any of the parts. It is preferred especially when precision fits are required. One of the biggest advantages of unilateral tolerance is the ease of inspection. As the dimensions vary on one side with the fixed upper values, it’s easy to standardize a gauge to increase speed as well as ease of inspection.
- Bilateral Tolerances: In contrast to unilateral tolerances, these tolerances are symmetrical around the base dimensions. This means both the upper and the lower limits deviate by the same value from the base or specified dimensions. As the name implies, the dimension may deviate in both the positive and negative directions. These tolerances are especially used for exterior dimensions.
- GD&T: The type GD&T or geometric dimensioning and tolerancing is superior to other tolerances types. This tolerance not only highlights the dimensions and tolerance of the part, but also outlines specific geometric characteristics such as positions, flatness, and concentricity. GD&T tolerances are mainly used for parts demanding extremely precise dimensions.
While designing the part, setting the appropriate machining tolerance is essential. This ensures the part will be created within the given specifications. This process seems easy, but in reality, it is not. It requires an in-depth understanding of machining tolerances and the different ways in which they are achieved for machines and materials. To get the tolerances made to your specifications, approaching a renowned, trustworthy, and experienced industry leader in machining and fabrication is always the best practice. Brogan & Patrick stands tall among its competitors. They are one of the well-known CNC machining service providers in the USA.
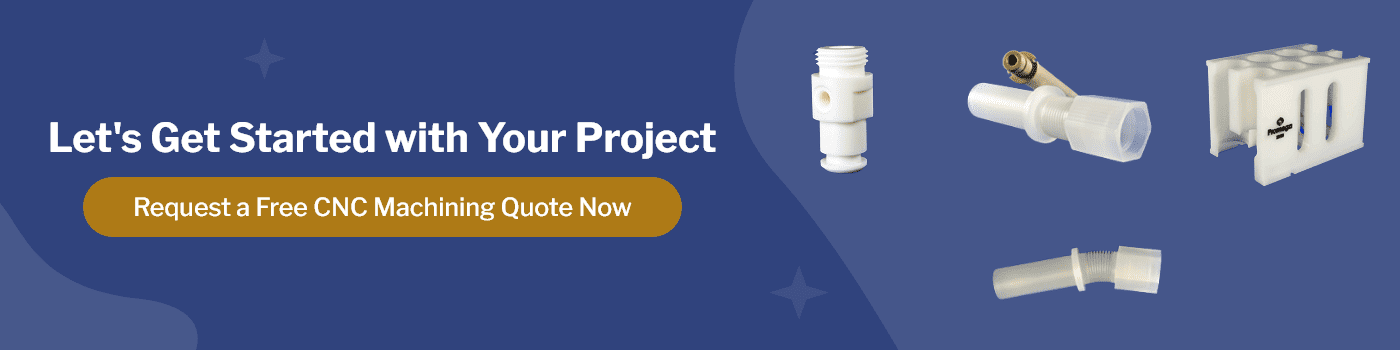